In the fast-paced world of industrial machinery and automotive engineering, precision, reliability, and efficiency are non-negotiable. Companies demand solutions that not only meet rigorous testing standards but also adapt to evolving technological demands. This is where hysteresis-based technologies and advanced motor testing systems shine, offering unparalleled performance across applications ranging from R\u0026D labs to high-volume production lines. Let’s explore how hysteresis brakes, dynamometers, clutches, and integrated motor test equipment are transforming industries.
THE SCIENCE BEHIND HYSTERESIS TECHNOLOGY
At the core of hysteresis devices lies a fascinating principle: the magnetic hysteresis effect. Unlike traditional mechanical systems that rely on physical friction, hysteresis technology generates torque through controlled magnetic fields. This mechanism eliminates wear and tear, ensuring consistent performance over time. The absence of physical contact between components makes these systems ideal for applications requiring smooth operation, minimal maintenance, and precise control.
HYSTERESIS BRAKES: PRECISION IN MOTION CONTROL
Hysteresis brakes have become indispensable in scenarios demanding exact torque regulation. These brakes excel in tension control systems for material handling, such as wire winding, textile manufacturing, and film processing. Their ability to maintain constant torque regardless of rotational speed ensures uniform product quality. For Smart web guide equipment , in the aerospace industry, hysteresis brakes are critical for testing aircraft component durability under controlled stress conditions.
Key Advantages:
- Zero mechanical wear for extended lifespan
- Silent operation in noise-sensitive environments
- Instantaneous torque adjustment for dynamic applications
- Immunity to temperature fluctuations
HYSTERESIS DYNAMOMETERS: THE GOLD STANDARD IN LOAD TESTING
When evaluating the performance of motors, engines, or turbines, hysteresis dynamometers provide unmatched accuracy. These systems simulate real-world loads while measuring critical parameters such as power output, efficiency, and thermal behavior. Automotive manufacturers rely on them for testing electric vehicle drivetrains, where precise energy recovery measurements are vital. Unlike hydraulic alternatives, hysteresis dynamometers offer rapid response times and eliminate fluid leakage risks.
Industry Applications:
- Electric motor certification for energy compliance standards
- Wind turbine generator testing under variable wind conditions
- Prototype validation for industrial robotics
- Battery performance analysis in renewable energy systems
HYSTERESIS CLUTCHES: SEAMLESS POWER TRANSMISSION
In automation systems requiring smooth engagement, hysteresis clutches outperform conventional options. Their ability to gradually transfer torque prevents mechanical shock, protecting sensitive gearboxes and drive trains. Packaging machinery, medical devices, and semiconductor manufacturing equipment benefit from their vibration-free operation. A notable case involves high-speed labeling machines, where hysteresis clutches maintain positional accuracy while handling fragile products.
MOTOR DYNAMOMETERS: BRIDGING DESIGN AND REAL-WORLD PERFORMANCE
Modern motor dynamometers serve as the bridge between theoretical designs and operational reality. These systems validate everything from miniature drone motors to massive industrial pumps. Advanced models incorporate regenerative power absorption, converting tested energy back into the grid—a feature increasingly important in sustainability-focused industries.
Cutting-Edge Features:
- Multi-axis torque and vibration analysis
- Integration with IoT platforms for remote monitoring
- Customizable test profiles mimicking actual operating cycles
- Real-time efficiency mapping across speed ranges
MOTOR TEST EQUIPMENT: THE BACKBONE OF QUALITY ASSURANCE
Comprehensive motor test benches combine dynamometers, sensors, and control software into turnkey solutions. From inrush current measurements to thermal imaging analysis, these systems provide a 360-degree view of motor health. Automotive suppliers leverage automated test stations to perform end-of-line quality checks on thousands of electric vehicle motors daily, ensuring defect-free products reach assembly lines.
Emerging Trends:
- AI-driven predictive maintenance algorithms
- Compatibility with hybrid and hydrogen fuel cell systems
- Portable test kits for field service diagnostics
- Cybersecurity protocols for data-sensitive industries
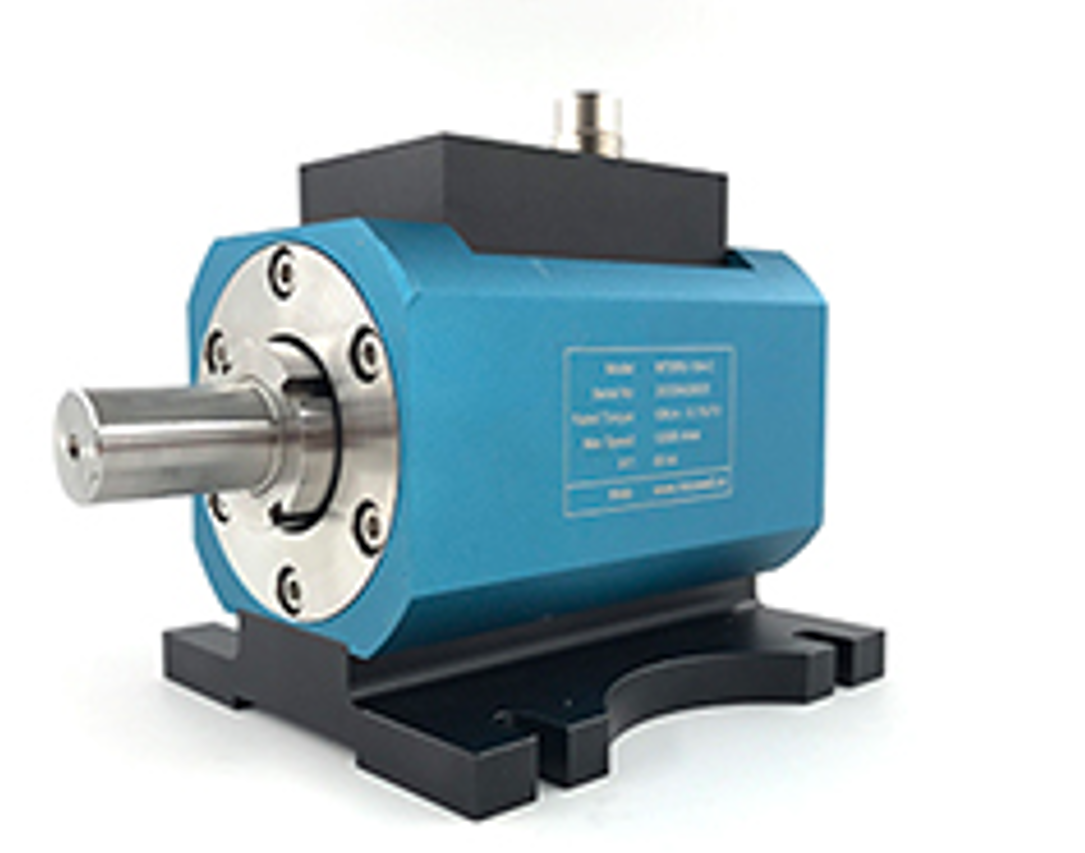
INTEGRATED MOTOR TEST SYSTEMS: SMART SOLUTIONS FOR SMART FACTORIES
The Industry 4.0 revolution demands interconnected testing ecosystems. Modern motor test systems synchronize with production line databases, enabling traceability from raw materials to finished products. Aerospace manufacturers, for instance, use these systems to maintain digital twins of aircraft engines, comparing real-time test data with simulation models to predict maintenance needs.
Core Capabilities:
- Automated pass/fail decision-making using machine learning
- Multi-protocol communication (CAN, LIN, Ethernet/IP)
- Cloud-based report generation with customizable templates
- Energy consumption optimization analytics
CASE STUDY: TRANSFORMING ELECTRIC VEHICLE PRODUCTION
A leading EV manufacturer recently implemented a hysteresis-based testing suite for their powertrain assembly line. The system integrates hysteresis dynamometers for motor testing, electromagnetic clutches for battery cooling system validation, and AI-powered diagnostic software. Results included a 40% reduction in testing time, 15% improvement in energy recovery during regenerative braking tests, and elimination of false-positive defect reports through machine learning algorithms.
CHOOSING THE RIGHT SOLUTION: CRITERIA FOR SUCCESS
Selecting optimal testing equipment requires careful consideration:
1. Torque/speed range compatibility with target applications
2. Data acquisition resolution and sampling rates
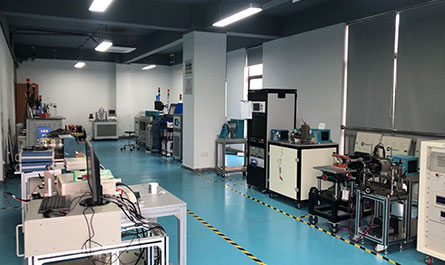
3. Compliance with industry-specific standards (ISO, SAE, IEC)
4. Scalability for future technology upgrades
5. Vendor expertise in sector-specific challenges
FUTURE HORIZONS: WHERE INNOVATION IS HEADED
The next generation of hysteresis and motor testing technologies will focus on:
- Ultra-high-speed testing for next-gen propulsion systems
- Quantum sensor integration for nanoscale measurements
- Self-calibrating systems using blockchain-enabled audit trails
- Hybrid testing platforms combining hysteresis and eddy current principles
As industries continue pushing performance boundaries, the synergy between hysteresis devices and intelligent motor test systems will remain crucial. These technologies not only ensure product reliability but also drive innovation by providing engineers with accurate data to refine designs. From reducing carbon footprints in manufacturing to enabling breakthroughs in renewable energy, advanced testing solutions are quietly powering the technological revolution—one precise measurement at a time.
Investing in robust hysteresis and motor testing infrastructure isn’t just about meeting today’s standards; it’s about future-proofing operations for tomorrow’s challenges. Whether optimizing existing processes or developing cutting-edge products, these systems provide the foundation for sustainable industrial growth in an increasingly electrified world.